汽車生產(chǎn)制造過(guò)程包含沖壓、焊接、涂裝和總裝四個(gè)工藝過(guò)程,依相關(guān)統(tǒng)計(jì),其中涂裝車間涉及加熱、冷卻、動(dòng)力、通信控制、照明等,能耗在整個(gè)制造生產(chǎn)過(guò)程中(沖、焊、涂、總)占比*大,所占費(fèi)用比例在70%以上。

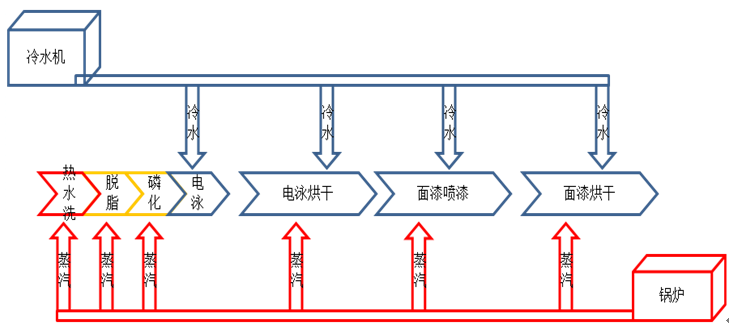
涂裝車間一般工藝流程為前處理、電泳、電泳烘干、面漆噴漆、面漆烘干等工序,工序中有加熱和冷卻等需求,至今常規(guī)加熱、冷卻能源幾乎都是燃?xì)庵苯蛹訜嵴羝ǜ邏簾崴厮┖屠鋬鰴C(jī)冷水。各需求之間獨(dú)立處理,沒有做能源回收再利用的整合處理,造成能源浪費(fèi),單產(chǎn)能耗高等問(wèn)題。
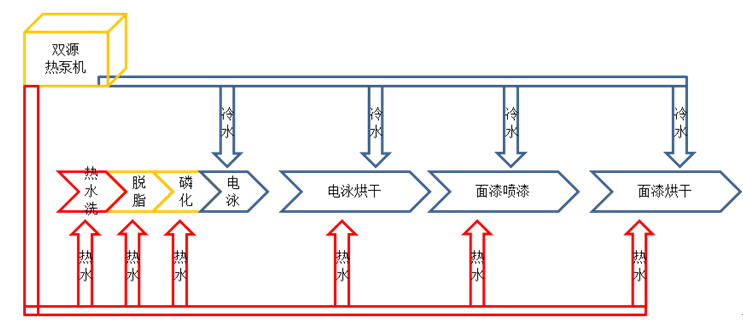
因此,要有效解決涂裝車間的能耗問(wèn)題,如何提升能耗的使用效率、降低無(wú)效能耗和能源的回收再利用是關(guān)鍵。隨著熱泵技術(shù)的發(fā)展,*高出水溫度可達(dá)90度,以及涂裝材料、涂裝工藝及設(shè)備的革新,涂裝工藝中熱能品位也逐漸降低要求,高溫?zé)岜贸鏊疁囟纫褲M足生產(chǎn)熱能品位需求。
熱泵作為從低位能源向高位能源傳輸熱量的設(shè)備,運(yùn)行效率COP高,且在運(yùn)轉(zhuǎn)過(guò)程中一定會(huì)產(chǎn)生低溫物品和高溫物品兩種產(chǎn)出,利用此物性正好滿足涂裝工序的冷熱需求,實(shí)現(xiàn)能能源綜合處理。
能源綜合處理,*大的問(wèn)題是冷熱需求不匹配,經(jīng)常出現(xiàn)冷需求多過(guò)熱需求或熱需求多過(guò)冷需求,造成系統(tǒng)不能穩(wěn)定運(yùn)行,雙源熱泵是以熱能需求為目標(biāo),采用空氣源和水源作為熱源的熱泵設(shè)備,有冷水需求時(shí),以水源熱泵運(yùn)行,實(shí)現(xiàn)雙產(chǎn)出,綜合COP高,當(dāng)冷水水溫低于某個(gè)值后,自動(dòng)切換到風(fēng)源熱泵運(yùn)行,確保熱能的產(chǎn)出。
實(shí)際案例,泰國(guó)某豐田汽車廠采用多臺(tái)宏星牌90度雙源熱泵機(jī)組(40STE-M390AHS4、40STE-N340AHS4)進(jìn)行涂裝車間能源綜合處理技術(shù)改造,經(jīng)實(shí)踐比對(duì),經(jīng)濟(jì)和減排效果良好。